Kingston on Compatibility
If Kingston knows inside-out, it's compatibility. Quite frankly we'd always thought it just "one of those IT myths" that IT managers spew to justify a fanboyism of a more expensive purchase. After all, memory is memory, right?
Well, after seeing it for ourselves, there's one thing Kingston is an expert in: testing memory on just about everything.
We went through Kingston's manufacturing complex in California, which does smaller job lots (like SDR and DDR memory) and process refinement before the refined methods are transferred to Taiwan, which does 30 per cent of the production, or Shanghai, which is a 24 hour operation doing the remaining 60 per cent (as California does 10 per cent).
California has four or five SMT lines at a cost of about a million dollars each, but the company as a whole has between 52 and 64 SMT lines depending on demand with memory and flash products shipping over a
million units per day.
The Main SMT room, with memory ICs progressively being attached to the PCB. Click to enlarge
Because of its size, it has enormous buying power with all the DRAM manufacturers, and this also gives it access to early/first samples of the latest ICs for testing. These get passed into its labs where they are assessed to conform to JEDEC specification, and a PCB is designed accordingly.
Finishing the memory. Click to enlarge
And the finished HyperX product (sometime later down the line). Click to enlarge
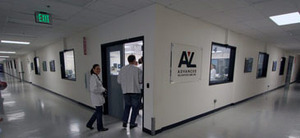
After that they're passed through environmental tests like humidity and temperature, etc to check the performance. An associate company called AVL (Advanced Validation Labs) on site takes care of this for Kingston. Unfortunately, we weren't allowed to take photos in there, just outside.
Finally the DIMMs go into just about every board imaginable in the market it's designed for: from server to notebook. Even if a product range is already out and the IC version changes, Kingston retests it completely to confirm compatibility. That's a lot of work! There are literally racks and racks of hardware in different rooms with labels hanging from the ceiling or stuck to desks labelled DDR3, DDR2, RDIMM, UDIMM, FB-DIMM, SO-DIMM etc
The main test floor: every product made gets passed through to be fully tested in actual machines before being sold. Click to enlarge
That's every-single-product it ships, not just reference samples. The products are finally tested in "typical" systems for the market they are designed for - this includes overclocked products in overclocked setups, too. For a company the size of Kingston that shifts a million units a day, this whole process quickly becomes mind boggling.
Kingston's attitude is that it doesn't want to see its memory come back. Some level of RMA is inevitable for any business, but a mass recall from incompatibility is unacceptable to them as it costs time to hand, money to replace and dump/fix stock, as well as the fact that customer opinion goes down the toilet too.
Kingston's brand new (in-house designed) automatic test machine loads DIMMs into real motherboards and tests them. On the right, the burn-in machines. Click to enlarge
Server memory is also artificially aged by three months in an oven to burn it in where Kingston claims it weeds out 95+ per cent of product death which constitutes to the majority of RMAs. It's not technology unique to Kingston,
Geil DBT for example does something similar.
Many thanks to Kingston and its staff for their time and insight into both memory and SSD technologies, not to mention letting us loose in its facilities!
Want to comment? Please log in.